Around the world, construction is generally impossible without suitable types of scaffolding. Built around buildings and in civil engineering projects, these temporary work platforms enable people, along with their tools and goods, to be transported safely along their multistory heights. This, in turn, will allow them to safely and efficiently complete tasks such as painting, plastering, and brickwork outside buildings. Scaffolds are also frequently utilized within buildings, enabling employees to access difficult-to-reach areas like ceilings or electrical installations.
Depending on the requirements of the construction workers’ tasks and the building standards they are working on, scaffolding is constructed in various ways. While bamboo or wooden scaffolding is a less expensive option in some nations, large-scale construction projects typically use other materials like steel or aluminum varieties. These metals offer superior strength and sturdiness and the ability to be developed to great heights. Although more expensive than steel, aluminum is frequently chosen as the material of choice for many different kinds of scaffolding. Because workers can more easily move aluminum because it is light. Therefore, aluminum scaffolds take less time to assemble and disassemble.
To rent a scaffolding, see Scaffolding Rentals.
Parts of Scaffolding
There are numerous distinct types of scaffolding. Depending on the specific layout of the scaffold, it is typically made up of one or more planks joined by various supports.
The critical components of scaffolding are listed below, along with descriptions of what each one does:
- Base jack: The base jack, often referred to as the soleplate, serves as the load-bearing base for the scaffold, which is made up of plates on the ground. It helps to support the vertical standards that are formed by the platform.
- Standard: which is also known as uprights are the vertical poles that make up the scaffold. They often comprise common types connected to the horizontal braces, called ledgers, forming scaffolding.
- Ledgers: are horizontal bracing that supports the scaffold’s standing platform and runs parallel to the wall.
- Putlogs: are horizontal braces that support the standing platform of the scaffold by running perpendicular to the wall.
- Transoms: Putlogs that cross over ledgers at their ends are called transoms. They carry loads by frequently supporting the boarding planks, also known as battens or decking boards, on which workers stand.
- Batten: Batten, also known as board or decking, refers to the planks that make up the standing area for scaffold workers.
- Brace: The scaffold’s overall structure is made firm by the diagonal tubes that make up the braces.
- Bridle: Bridles are horizontal supports that bridge openings.
- Couplers: Fittings that connect the various parts of a scaffold are also known as couplers.
- Scaffold tie: The scaffold is fastened to other structures using scaffold ties.
- Guard rail: On scaffolds, guard rails are one safety barrier. They prevent workers from unintentionally falling from the platform and are generally about one meter in height.
- Toeboard: Toeboards are another form of protective measure on scaffolds. They are exceptionally short vertical barriers that give workers a sense of their position on the platform concerning its edge. They also help to prevent implements like screwdrivers from slipping off the edge of the boards.
Some scaffolds have different ladders or stairways to make it simpler for workers to board and depart and occasionally overcome physical limitations while on the scaffold. Other people might also have trash chutes for securely removing waste from the scaffold.
Using these essential parts, contractors and workers build specific scaffolding types to suit their needs. We take a look at the usually used scaffolding types below:
Types of scaffolding
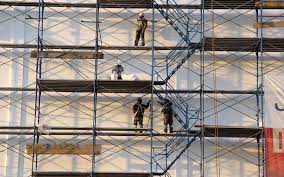
Tubular and Walkthrough Frame Scaffolds
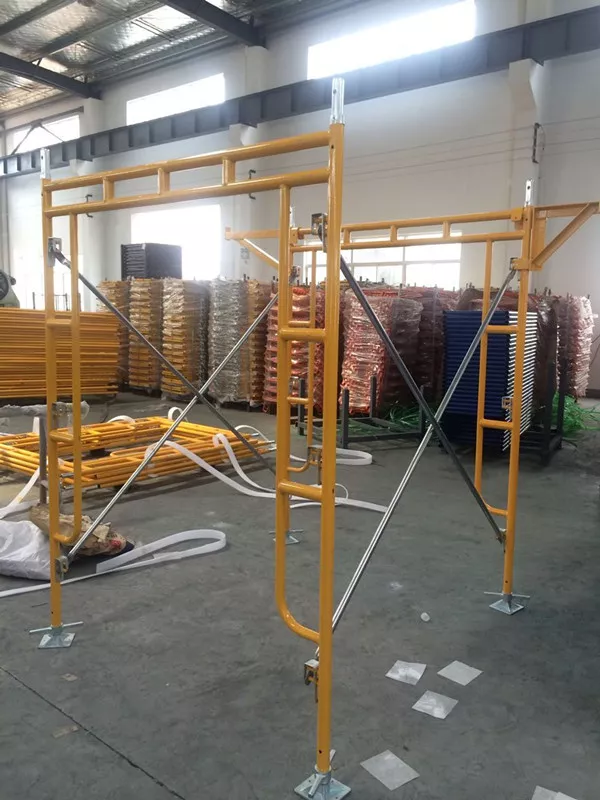
One of the most fundamental types of scaffolding is the tubular frame scaffold, which may be shaped to the lengths and configurations required for a specific building project.
While steel frames are standard, Also quickly gaining popularity is aluminum tubing. Because the metal is lightweight, workers can assemble and disassemble it quickly. Ladders are frequently attached to or integrated into tubular constructions. However, staircases or ladders with additional safety features are advised for high-rise scaffolds higher than 30 feet.
The walkthrough frame is a variant of the tubular frame scaffold with high platforms that provide the uninterrupted movement of personnel, bystanders, and/or materials below.
Rolling Scaffolds
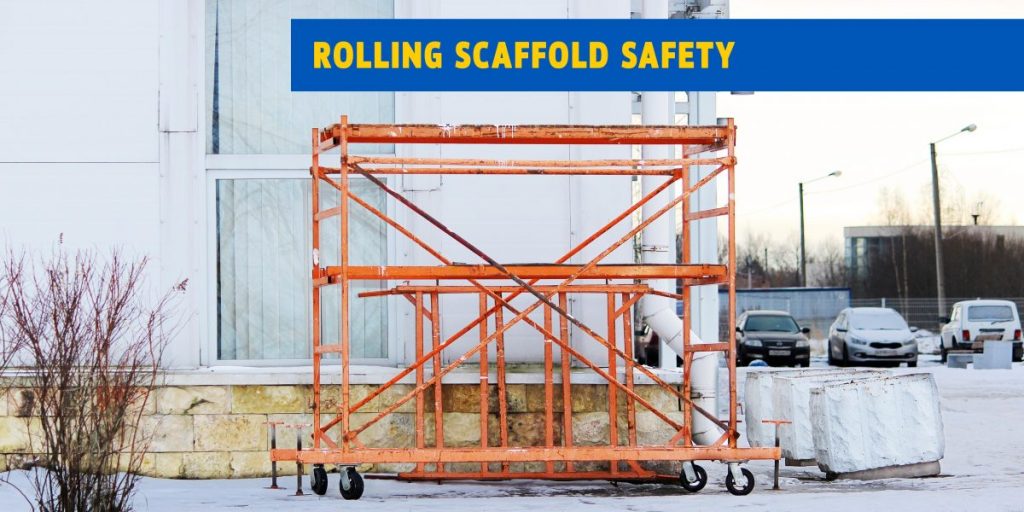
Rolling scaffolds are, quite simply, scaffolds on wheels, frequently used for interior building work like electrical installations or wall painting. These projects call for the same-sized platforms for short durations at multiple locations; wheels enable one scaffold to be conveniently transported wherever needed. Of course, these scaffolds are equipped with brakes to firmly park them where required.
The farm wagon scaffold is a variant of the rolling scaffold hoisted over a machine with tires. This is typically used for external or industrial buildings, often sheet metal siding and similar materials.
Tube and Clamp Scaffolds
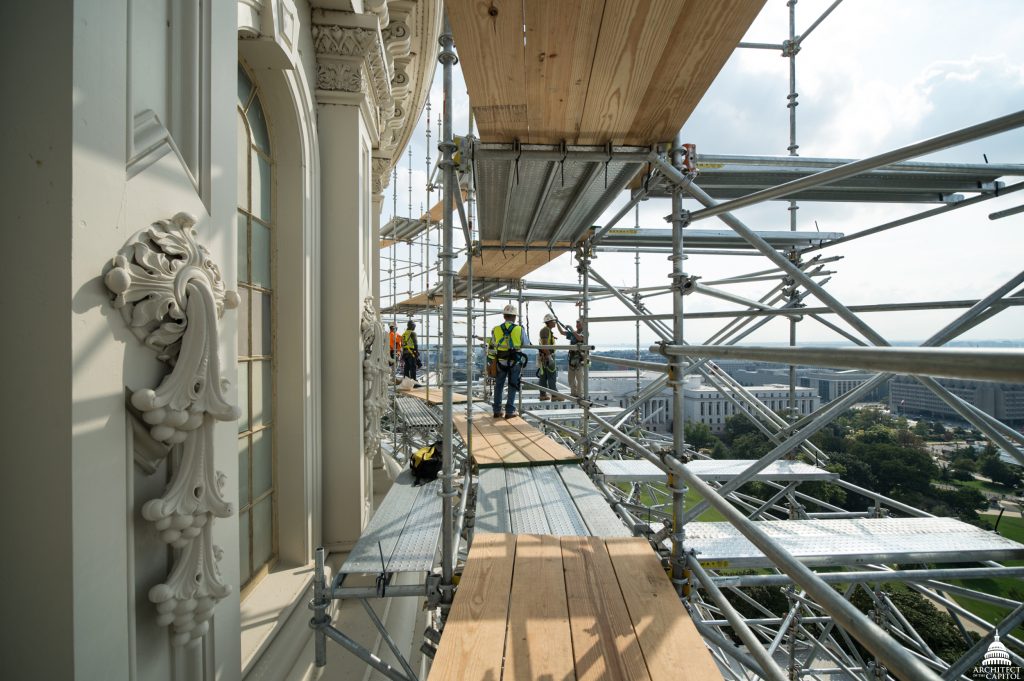
Due to its flexible structure, tube and clamp scaffolding is one of the oldest types of steel scaffolding. Consists of two parts: clamps and tubes, also referred to as couples. This structured style is simple to assemble and may be shaped as you choose.
Construction workers must use the couplings to join the vertical and horizontal tubes and build any type of scaffolding structure, regardless of height, width, or shape.
This makes tube and clamp scaffolds particularly advantageous for buildings where impediments prevent using more linear scaffolding types.
Systems Scaffolds
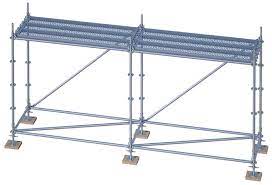
Systems scaffolds are different kinds of flexible scaffolds that use prefabricated horizontal and vertical sections to provide the structure needed for a construction job. They can be utilized for non-linear, round, or dome-shaped constructions even though they are less pliable than tube and clamp scaffolds.
Systems scaffolds are manufactured in wide varieties, such as steel versions for heavy loads and lighter aluminum ones for smaller repeated scaffold structures.
Galvanized steel is used in Cuplock systems scaffolding, with connection points (referred to as clocks) spaced consistently every half-meter to a meter. This makes it perfect for developing repeatable, standardized systems.
Staircase towers are another common design of scaffolding system that enables workers to travel quickly between levels. These come in handy when employees require short-term, secure access to a particular building area.
Suspended or Swing Set Scaffolding
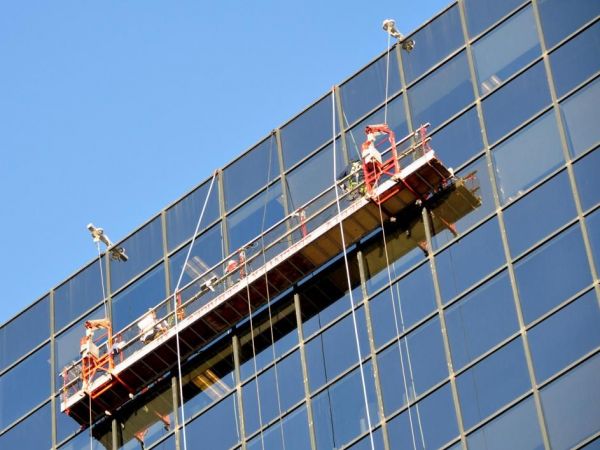
For exceptionally high-rise buildings or for construction work involving the upper stories of a building, contractors prefer to use swing set scaffolding suspended from a building’s roof. Compared to other scaffolding kinds constructed from the ground up, this is considered a more practical and affordable option.
A swing set scaffold consists of a scaffold that may be raised or lowered by an external crane, an electric motor, or a cable pulley system, depending on the height of the building. However, the platform height of some swing sets is fixed and cannot be changed for positioning purposes.
Scaffolds for swing sets are best suited for small-scale tasks like rapid maintenance like painting. Still, longer-term jobs can use heavy-duty kinds.
Mast Climbing Scaffolding

Moving along a fixed tower constructed from the ground up, a mast climber can change its position along a building’s height, similarly to swing set scaffolding. An electric motor or a gas engine power the platform. Depending on the project, the tower’s height can range from a few floors to several stories.
An obvious advantage over swing sets is that they can bear a large load. And their position can be minutely adjusted, which comes in handy for brick or block-work. Another benefit of mast climbers is that they can be accommodated in construction sites with limited area as they do not take up a lot of space on the ground. However, depending on the work’s scale, they may contain more than one tower.
They work best for projects with a medium to high height. They are used by workers while plastering walls, adding siding, or windows. The mast climber frequently features distinct platforms for employees and supplies at various heights, which makes it easier for the workers to operate ergonomically.
H Frame Scaffolding
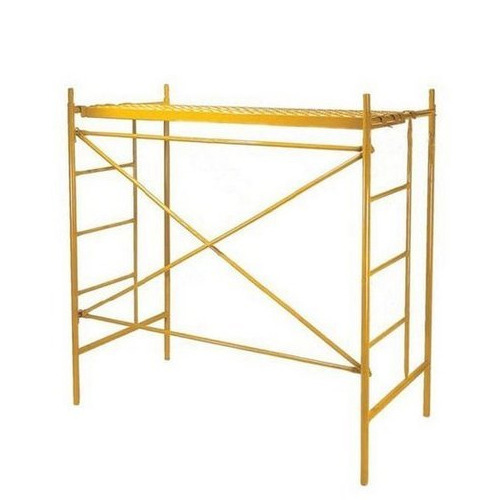
What is H Frame Scaffolding? In its most basic form, this scaffolding system is used for interior plastering projects like walls and facades. The other uses are painting, insulation, facade cladding, and building and repairing ships.
Another detail about H Frame Scaffolding is that it is divided into three parts: vertical, horizontal, and diagonal. Comfortable and dependable is the H Frame Scaffolding system. By establishing rigidity with the connections, it is additionally resistant to buckling. Further, it includes secure spaces where you can transport loads.
What is H Frame Scaffolding? Where To Used It?
H frame scaffolding guarantees that you save time and effort because of its characteristics. Essentially, the system is made up of linked frames. The height of an H frame is 2 meters, and the distance between them is 2.5 meters. In this system, auxiliary components are also employed.
- Metal plank
- Stairs with or without landing
- Adjustable base jack
- Adjustable support
The scaffold is more robust and safer thanks to steel working platforms. Passageways between feet are safe inside scaffolding with some applications such as a staircase or access ladder. The use of scaffolding clamps in jacketing ensures scaffold safety and makes its application easier.
Properties of H Frame Scaffolding
The system is made of TS EN 10219-1 approved tubes, frames measuring 48.3 mm by 3.0 mm, diagonal elements measuring 42 mm by 2.5 mm, and horizontal components measuring 34 mm by 2.0 mm. Working platforms are created using a roll-forming machine with a carrying capacity of 300 kg per square meter. The system has galvanized hot-dip according to TS EN 12811-2 specifications.
Usage Areas of H Frame Scaffolding
H frame scaffolding is a simple tool that can be used to build a variety of constructions, including:
- Within homes and tall buildings
- In commercial and retail establishments
- at underground and subway stations
- In commercial structures
- Energy-related facilities
- In healthcare facilities like hospitals
- In slabs for bridges and viaducts
- projects for hydroelectric plants
In general, the system is preferred for tall and thick slabs. It is made up of two components: ledgers and an H frame. All aspects of the system can be installed with human power. Gaps of the tower are adjusted by calculating slab loads compatible with the project.
Is scaffolding dangerous
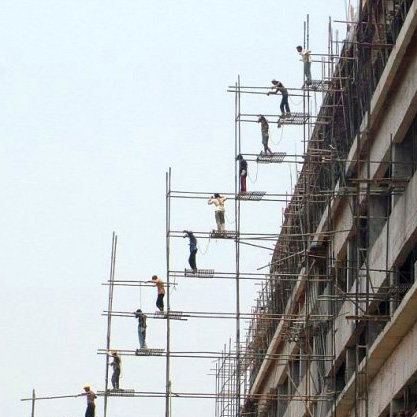
reasons for scaffolding accidents
Scaffolding is a temporary structure that lets workers move more freely and reach heights than they could if they were merely utilizing a ladder. Construction workers in almost every construction industry employ scaffolding to build new buildings and repair existing structures.
While using these structures, workers face many dangers and are at an increased risk of injury. Workers performing construction, maintenance, or repair at any height are already at risk for injuries. The following are some of the most frequent causes of scaffolding accidents:
Improper scaffold construction: when scaffolding is not built or maintained correctly, it can lead to accidents and injuries.
Scaffolding not properly inspected: Concerning building scaffolding correctly, A construction sector employee who has received specialized training must do these inspections. They will need to understand the specifics of scaffolding, including how it is built and maintained.
Falling objects: Things like tools or bits of construction material being dropped cause many accidents on construction sites. People below may suffer serious, even fatal, injuries if an object is descended from a scaffold.
Any one of the following scaffolding-related issues can result in an accident in addition to these several kinds of scaffolding accidents:
- Inadequate Safety Procedures
- Insecure or non-existent bracing
- Weak planking
- Insufficient training
- Lack of protective equipment
Sources:
- https://saudiscaffolding.com/blog/scaffolding-parts-and-scaffolding-types-in-construction/
- https://www.gurbuziskele.com.tr/what-is-h-frame-scaffolding/
- https://brandsafway.com/tube-and-clamp-scaffold-supported-scaffolding-systems
- https://www.kieklaklawfirm.com/why-is-scaffolding-so-dangerous-on-the-construction-site/
My brother’s buddy recognizes the need of having sturdy and secure scaffolding equipment as he gets ready to start a significant building job. He makes the decision to search for a reliable scaffolding rental provider in order to guarantee the project’s smooth progression and the workers’ safety. He ought to inform him that aluminum tubing is increasingly overtaking steel frames as a preferred alternative. Workers can swiftly construct and remove it since the metal is light.
It’s good that you mentioned that scaffolding helps construction projects that need work like painting and plastering to be done much easier since it enables workers to use the platform to transport safely along multistories with their tools. I recently bought an old commercial building with four floors that I wanted to turn into an apartment complex soon, so I’m getting it renovated next month. I’ll make sure to hire a reliable scaffolding company in Illawarra to help us with the renovations soon.